When considering more environmentally friendly battery packs, sustainability has to be a key objective from the outset. “With sustainability, you have to have the end game in mind before you actually start,” says Douglas MacAndrew, chief technology officer at InoBat. Material choice is also crucial: “At a cell level, a natural assessment needs to take place where you’re using materials that are able to be recovered. And those that can be economically recovered.” Lithium nickel manganese cobalt oxide (NMC) materials do create some value when they are being recovered. “We successfully took an essentially 622 chemistry material through a mechanical and electrochemical recovery process and turned it into an active 622 material again,” says MacAndrew. “We benchmarked that with virgin materials: it performed extremely well, with 95% performance of the virgin material.”
“The industry is moving from 622 to 811 NMC chemistry (80% nickel, 10% manganese and 10% cobalt),” reports Dr Doron Myersdorf, CEO of StoreDot, whose extreme fast-charging (XFC) technology aims to extend the lifespan of batteries, helping second life and delaying the need to recycle. “We are trying to avoid using cobalt as much as possible,” he says. Substituting ‘precious’ materials with elements more abundantly found in the environment is another vital step: “We are replacing graphite with silicon, which you don’t need to mine. It’s the second most abundant element on Earth. We do process it but in terms of the material itself, we eliminate the need to mine carbon.”
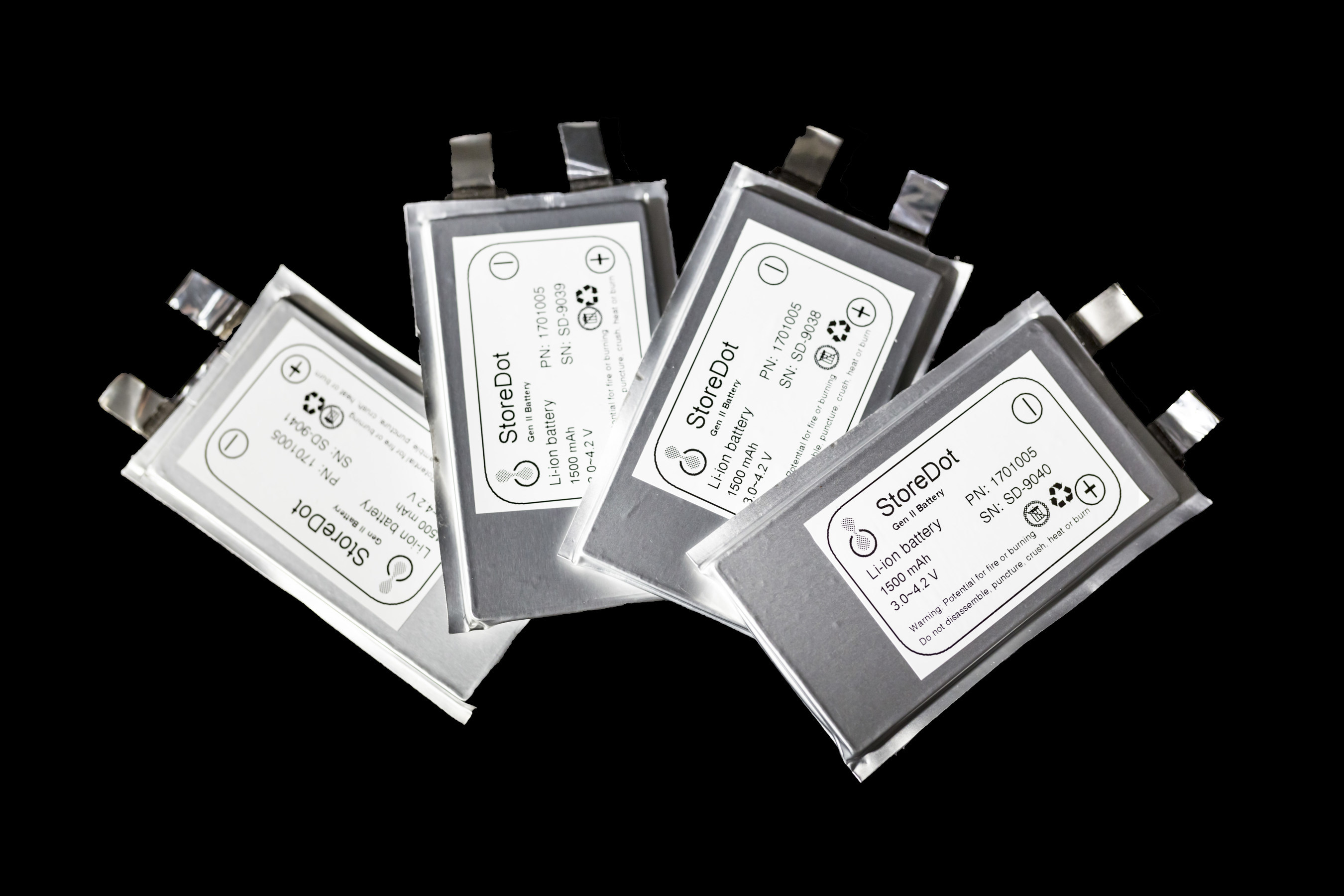
However, the use of lithium, which needs to be both extracted and reused, is an industry-wide issue: “Lithium is the most effective element for storage of the ions. Because it’s the lightest metal, it can transfer the ion into the active material more easily.” Something else that needs to be introduced is an easier process to check the battery’s state of health (SOH), according to Andrew Abbott, a professor at Leicester University in the UK and a researcher on the Faraday Institution’s ReLiB battery recycling and reuse project: “It’s about having quick and simple diagnostics to tell the battery SOH. For example, what the actual maximum capacity of the cell is. When a vehicle comes in for triage, an analysis of its SOH can decide if the battery can go for second use or if it needs to be recycled.”
Designing-in ease of disassembly from the start of battery development to enable easy recycling is a key step in the sustainability process, says Beatrice Simonsson, head of product management at Polestar. “Technically, all batteries can be recycled to a very high efficiency regardless of design, but recycling is most efficient when the waste is pre-sorted. Designing for ease of disassembly of battery components is a great focus for us, as it makes it easier to separate the different materials (aluminum, copper, electronics and cells) before they enter a complex pyro/hydrometallurgical process, which requires energy and many steps to extract the constituent materials.”
Improving the ease of assembly/disassembly makes battery repair more cost-effective and sustainable too. “Designing a battery pack with accessible and replaceable components is highly important to repair it,” Simonsson reports. “If this is not possible, we have collaborations to remanufacture batteries – a battery is designed to be repaired, remanufactured, reused and recycled.” Abbott reports that many batteries have a minimum life of 12 years, sometimes even more: “In the Far East, there is talk about a ‘million-mile’ battery that can go through several hundred cycles without any significant decreases.” Cell type and chemistry play a part here: “In the West, chemistries are mostly based on NMC. In the East, there is a move toward LFP chemistries, which are cheaper in principle as they don’t depend on scarce materials, but the power densities are significantly lower.”
Irreversible binders
With increased power density, the amount of ‘dead’ material in a battery cell can be minimized, Abbott reports: “We can then move away from irreversible binders. Some manufacturers use very large volumes of epoxy or polyurethane resins to stick small cells together [see Premium bonds, left]. They lend structure and strength to the powertrain but at the end of life, the number of cells per unit volume decreases. Pulling the cells apart is also impossible. It’s trying to work out that happy medium – if you can get bigger form factors in cells with less adhesive use.”
MacAndrew says that battery longevity very much depends on the application and the nature of how the batteries are operated. “With our optimization processes, we look very carefully at the chemistry design for life and the cell to make sure we’re extending life as much as possible,” he reports.
StoreDot is completing at least 1,000 consecutive fast- charging cycles, says Myersdorf, which is important for second life: “The more cycles you have, the more sustainable the battery is.” Abbott believes legal problems associated with second use are one reason why batteries are not reused very much. The design of some battery packs don’t lend themselves to being taken apart very easily, either. “You want something that is easy to split up,” he says. MacAndrew believes that second-life use is now being designed into new battery packs: “We’ve tried to ensure we have a modular approach to how we put cells into installations, where those modules that have a service ability can be extracted – they’re not installed and never to be taken out again.” “We plan for the second life of the battery,” says Myersdorf. “Most battery technologies will continue to drop rapidly and don’t even suit second life. We can plan the battery cycling so even after 80% it continues to give good performance, until it gets to 60 or 70%.”
Traceability in the supply chain is also important to create more sustainable battery technology. “We’ve implemented a system that maintains the circular economy from the raw material until it’s recycled, and are partnering with organizations that provide this data,” says Myersdorf.
“Data is very important, so we know these materials are not being dumped in landfill and they are being used first for second life, and then being properly recycled.” Simonsson confirms that shared material sustainability issues are key. “We work closely with our battery suppliers on our shared material sustainability issues – climate, circularity, traceability and responsible sourcing. We have a unique collaboration with our battery suppliers on lifecycle assessments [LCAs], enabling us to create a shared view and an action plan on climate emissions sources stemming from battery production,” she says.
This transparency enables Polestar to present a carbon footprint for the battery within its model LCAs. To design more sustainable battery packs, MacAndrew believes that the complete value chain, the entire cycle and the circular economy associated with batteries must be looked at holistically: “Within our processes, this includes the recovery of materials from our battery scrap – manufacturing processes inherently produce scrap – and we have an expectation our recycling will be as much in our control as it can be. That ultimately gives us a very close connection to material use that comes from our processes, also altering materials that come from battery end-of-life recycling.” Abbott says, “We’re looking at ways to short loop recycle materials, especially upcycling materials to get higher value into them. We came up with a process that we’re now trialling with one OEM, using ultrasound to delaminate production scrap. We’ve got a very efficient process recycling technology similar to what happens when you have the ultrasonic pick on your teeth at the dentist – you put the electrode underneath it and it just strips all the active material off very, very quickly.”
Circular approach
“We also want to make sure the recovery of materials reduces the demand on mining as much as possible,” MacAndrew states. “We see a significant spillover benefit of actually understanding how we can economically close the loop, and have materials coming out of and going back into batteries, rather than going into other uses or into landfill. We have a circular approach in mind when we look at how we define our product.” InoBat takes end-of-life batteries out of the marketplace, replacing them with upcycled batteries. The cradle-to-cradle technology the company uses turns scrap material from waste batteries, sourced from old EVs and gigafactories, into cells with a lower CO2 value.
Myersdorf believes that with demand growing for EVs and therefore batteries, OEMs, technical partners and vehicle buyers are beginning to realize the importance of battery sustainability and recycling. “One of our investor partners, Polestar, puts ‘green’ and recycled materials at the top of its battery design parameters,” he says. “We are also designing these vehicles for Generation Z, who care about the environment. This is a critical parameter when they buy a vehicle – whether the components within that vehicle are aligned with their lifestyle and values regarding the planet and sustainability.”
Future battery chemistries and emerging technologies may shift, but in the medium to long term, MacAndrew believes that NMC will still be the core underpinning of mobility: “It has the capability of delivering power and gravimetric capacity that makes it difficult to compete against.” Other technologies – including solid state – will also play a part: “There are other chemistries we’re working on to make sure they are also able to benefit from our development process. “Lithium iron phosphate [LiFePO4], lithium manganese iron phosphate [LMFP] and lithium titanium oxide [LTO] chemistries all have a natural benefit of being able to be optimized in the way that we design our cells and chemistries for our customers’ needs.” Pressure to reuse and recycle materials is only going to increase as the drive towards sustainable electrification accelerates.
Premium bonds
One of the most pressing issues for battery pack disassembly is the use of bonding materials. “If you look at the teardown of some cars, even Teslas, it’s very, very difficult to get to the battery itself because of the epoxy and the glue that are put inside,” says StoreDot’s Dr Doron Myersdorf. These adhesives make disassembly down to cell level difficult. “Debondable adhesives are a hot new topic,” Leicester University’s Andrew Abbott says. “We’ve done some work on trying to make epoxies that come apart on request. What you do is put a switch in that allows you to have a stimulus, either thermal, light, magnetic or whatever it is, which allows you to cause the glue to unbond itself.”
The use of small, 18650 cylindrical cells in older applications isn’t helping matters, as they need to be stuck together to match the energy density of larger prismatic cells. “Overall, we need to move to larger cells,” Abbott states. Processes that include building structure into the bus bars rather than through the use of structural adhesives may help. “As new battery architectures come, that are designed to be able to be pulled apart rather than shredded, what you can get to is more efficiently recycled, more purified and separated materials,” he says. “We are about to publish some new work on ways in which you can design the cell to use as little adhesive as possible, and be able to be pulled apart,” Abbott continues. “There are moves afoot but there are conversations to be had with OEMs.” Abbott also reports that there is a need to move away from perfluorinated binders. “These perfluorinated compounds are finding a use in batteries because of their stability. However, they create all kinds of problems. If we could get to water-dispersible binders inside the cells for both anode and cathode, that would revolutionize recycling.”