The automotive industry has reached a tipping point. Historically, government and consumer interest in vehicle emissions has focused almost exclusively on public health. From the US Clean Air Act of the 1970s, which drove the introduction of catalytic converters, right through to the ongoing saga of Dieselgate, tailpipe emissions have always taken center stage.
But not anymore. Electrification means that localized tailpipe emissions are no longer an issue for a growing number of vehicles. Instead, global greenhouse emissions and primary energy use have shot to the top of the agenda. For electric vehicles this becomes a complex and sometimes divisive topic.
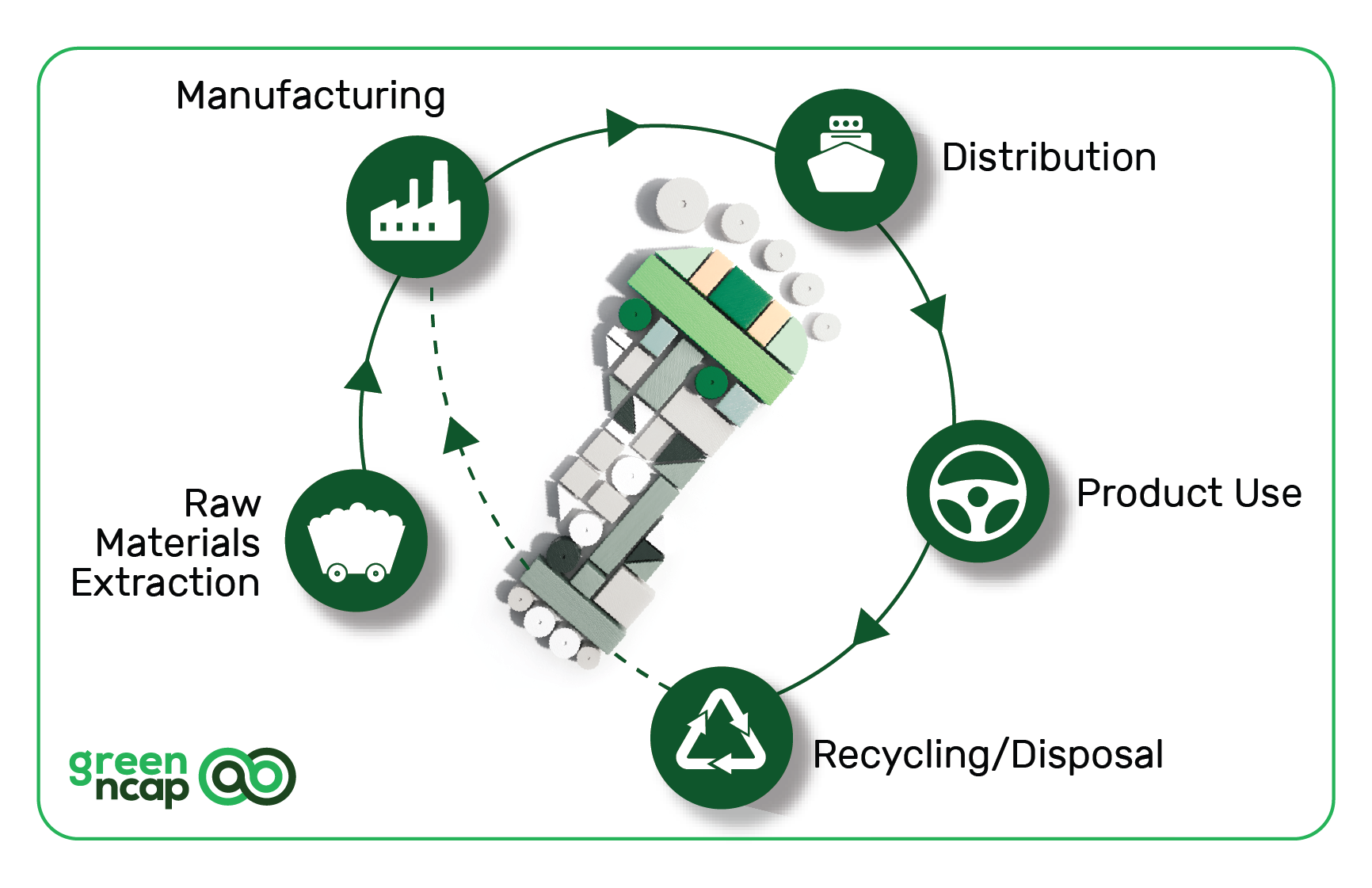
EV skeptics have long delighted in cartoons of electric vehicles plugged in to coal-fired power stations, belching out black smoke. And while that may be a grossly over-simplified representation, it taps into a fundamental truth that there’s more to a vehicle’s environmental impact than its localized emissions. In theory it’s possible to calculate any product’s total lifecycle emissions, whether you’re talking about a car, a T-shirt or a toaster.
The lifecycle assessment (LCA) process starts with raw material extraction and transportation, progresses through manufacturing and usage, and finishes with end of life and recycling. This holistic approach is arguably the most relevant way to assess a vehicle’s environmental credentials. And it’s perhaps the only way that technologies as diverse as battery-electric storage, fuel cells and internal combustion engines can ever be directly compared with one another. However, it’s also fraught with peril. As one of our interviewees for this feature put it, “Measuring real-world NOX emissions from a combustion engine is a walk in the park compared with quantifying the CO2 emissions from a battery mining chain.”
So what are the principal challenges involved in producing an automotive LCA, what needs to be improved, and will it ever be possible to do it with sufficient accuracy to compare one vehicle with another?
Varying scope
The term ‘lifecycle assessment’ covers a broad range of studies, intended for different audiences. Typically the focus is on greenhouse gas emissions and energy use, although some analysts look at factors such as toxicity, water consumption and eutrophication. Some don’t even look at the environmental aspect at all, but instead consider the socioeconomic impacts of the supply chain.
Broadly speaking, automotive LCAs are aimed at three distinct groups: consumers seeking to make a more informed choice on their next purchase, policymakers in local or regional governments and members of the automotive industry either carrying out internal reviews or publishing their data for a wider audience.
“We know that a lot of manufacturers already have their own LCAs or are working toward that,” comments Aleksandar Damyanov, technical manager of Green NCAP. “Some of them see this as a chance for better market positioning. Others may hope that [demand for LCAs] will just pass, but I can assure you it will not. They are something that we will see more of in the future, so the quicker manufacturers respond, the better selling argument they will have.”
Earlier this year, Green NCAP began publishing its own independent LCA reports. The are primarily aimed at consumers looking to investigate general trends in the market. For instance, such a report can give a good indication of how a battery-electric vehicle might compare with its hybrid counterpart or whether a large SUV would have a greater impact than a small hatchback.
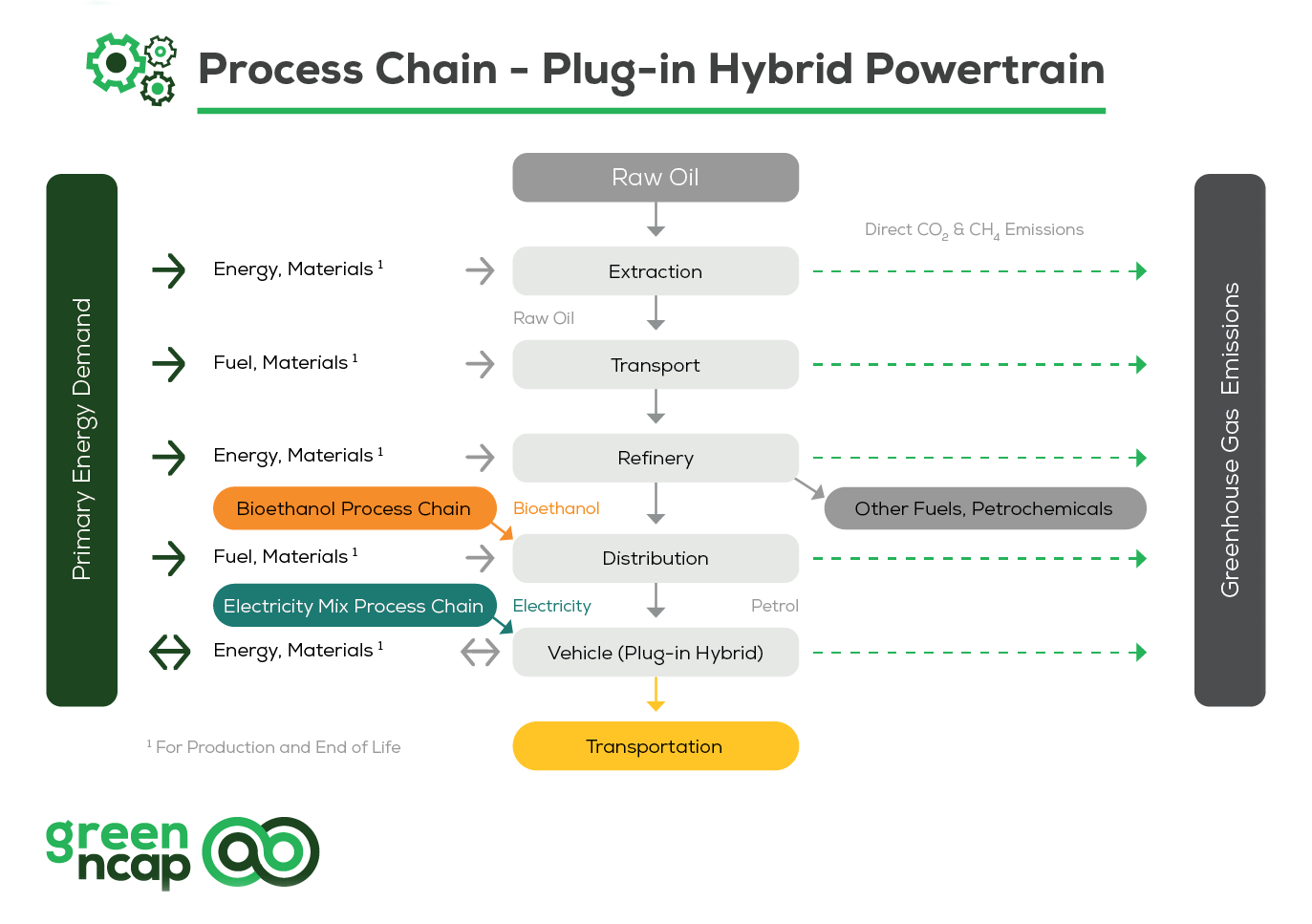
However, they are not intended to give precise figures at this stage. “We believe that lifecycle assessment is the best way to quantify the impact of a product. But it’s still an estimate and we’re talking about a range of figures for each vehicle model,” comments Damyanov. “If two models are very close together it’s not currently possible to say which is better. On the other hand, if the results are substantially different, and you can identify which phase of the lifecycle accounts for that difference, then you can make a sound generalization.”
As with most automotive LCAs, Green NCAP’s assessments are based on the internationally recognized ISO 14040 and 14044 standards. These set out the basic framework for the reports, but they don’t describe the methodology in detail. Green NCAP has put together its own system, based on the LCA Expert Tool developed by Austrian technical institute Joanneum Research. However, establishing a methodology is only the first part of a far more complex problem. “The really important point is where the data comes from and how trustworthy it is,” notes Damyanov. “Having the right structure and methodology is meaningless without good-quality information.”
Green NCAP divides this information into two categories. Foreground data relates specifically to an individual vehicle, such as its mass, battery capacity, lifetime and charging type, and these account for much of the difference between one car and another. Background data is more generic and tends to vary less between designs and manufacturers, such as the environmental impact of the steel or aluminum used in a vehicle’s construction. “In most cases, the background data is based on information that cannot easily be measured directly,” comments Damyanov. “For instance, the greenhouse gas emissions of oil extraction or battery production. Due to lack of data it is not yet possible for us to address these individually for each model or manufacturer, so generic LCA data from various databases is used, such as GEMIS and ecoinvent. As most of the background data from LCA databases cannot be published explicitly, priority is given to Joanneum Research’s own models and calculated background data.”
These are global figures, he points out: “We can’t differentiate between a tire produced in Asia and one produced in the US, for instance, but it’s important to note that they are very good estimates when it comes to a global average.” Nonetheless, much of the model-specific data can be measured precisely.
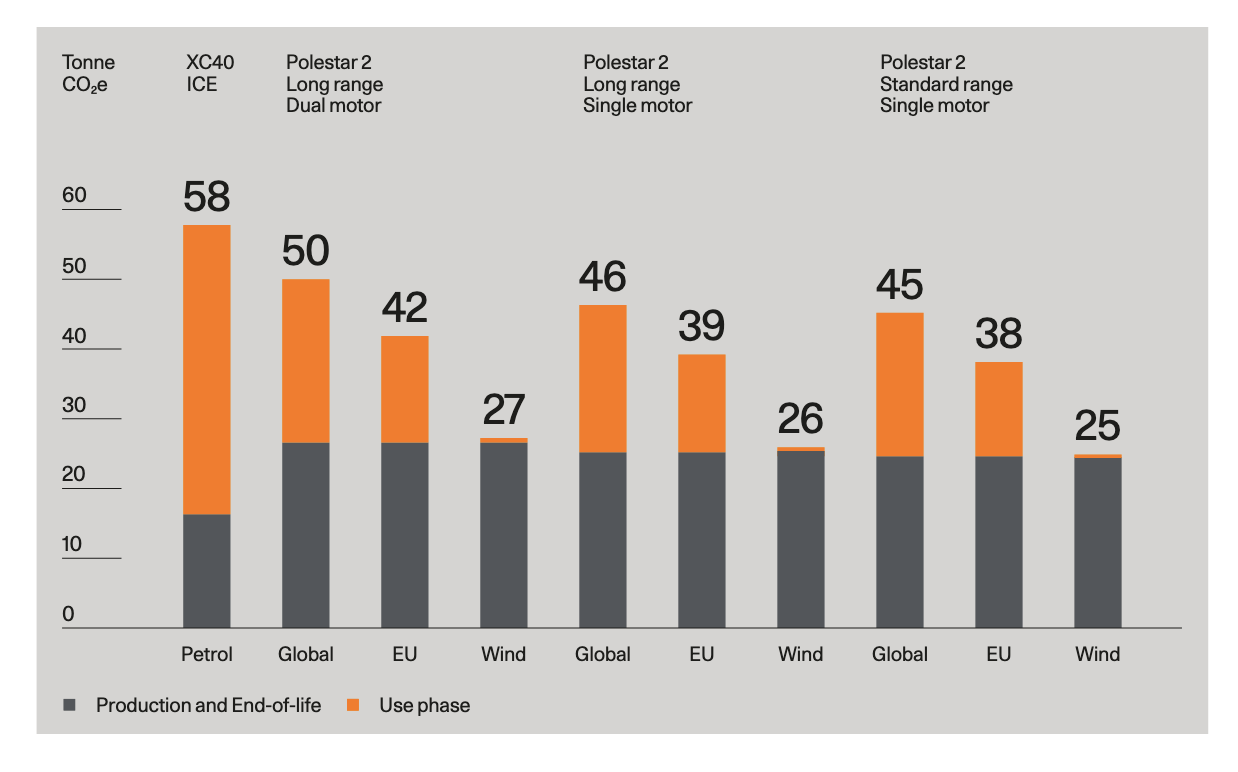
Factors such as vehicle mass, battery capacity and energy use, for instance, are already incorporated into Green NCAP’s reports. But to go beyond that will require more detailed information from the manufacturers and suppliers. “In the future we would like to go into enough detail to allow one model to be compared with another,” says Damyanov. “To work toward that we are pushing manufacturers to deliver us their own LCA analysis, or at least a bill of materials of their products and how they are produced. For instance, where they’re made, where the materials come from and how much of that is recycled [both at the beginning and end of a product’s life].”
One possibility is that these manufacturer-supplied LCAs could be self-certified under the guidance of an external auditor who would ensure that the correct data and methodologies have been employed. Damyanov says he’s hopeful that the global nature of the industry and the breadth of different stakeholders involved means that a common methodology could be established that would provide a balanced view. “If Europe, for example, could establish the methods and a framework to provide this information, and as long as there is no room for cheating or manipulating results, then I’m confident it could be done. But it’s too early to say when,” he notes.
Different methods
Not everybody is convinced. Nick Molden, founder and CEO of Emissions Analytics, agrees that lifecycle analysis is a logical way to track the environmental impact of EVs, but questions whether it’s practical. “We’ve done a high-level review on all the LCA models held in the British Library, and we came away with two observations,” he comments. “The first was that you can get almost any answer you want, depending on the model you choose and the assumptions you make. The second was that certain critical pieces of information are very hard to validate. If you want the true CO2 emissions of a cobalt mine in the DRC or a graphite refining plant in China, for instance, it’s very hard to independently verify any claims.”
Professor Darek Ceglarek, director of the Digital Lifecycle Management Group at Warwick Manufacturing Group (WMG), agrees: “The basic LCA procedure is, in principle, relatively straightforward, but it can become extremely complex because it can involve dozens of separate processes as well as hundreds of tracked substances. Such is the level of complexity that there are a number of studies that even disagree on whether EVs are more or less harmful than ICE vehicles.”
The industry is working hard to address these issues. Swedish automotive manufacturer Polestar, for instance, has embarked on a project with supply chain specialist Circular to digitize and track its materials using blockchain. The auto maker has also led calls for a common LCA framework and greater transparency on the assumptions that are made when OEMs and suppliers compile their own reports.
Chinese EV specialist Nio has also been working on its own sustainability plan. The firm’s Nio Factory 2 plant in Hefei is equipped with sensors to record and analyze its energy consumption and carbon emissions, with a quarter of its electricity now coming from solar panels on the roof. “We’re working with our supply chain partners to evaluate the carbon footprint not only of our vehicles, but also of the parts and components,” says William Li, founder and CEO of Nio. “We’re gradually building up systematic and complete capabilities together with our partners. Regarding an LCA, we are still working on the data and will release it at the appropriate time. It takes considerable time to calculate the information from the whole value chain.”
For EVs, most of the environmental impact comes from the materials production phase. According to Polestar’s recent LCA report on the Polestar 2, the lithium-ion battery was the joint highest contributor to its materials impact (tied with the steel at 29%). It is also one of the least understood contributors. “If you were doing a lifecycle analysis to compare one combustion-engined vehicle with another, you already have very robust models for the steel, aluminum, plastics and so on. The mystery black hole of information is the battery,” notes Molden.
Track and trace
Even for OEMs, tracing this data down the entire value chain can be complex. What’s more, it can include commercially sensitive information that they may be reluctant to share outside their organizations. In the EU, data-sharing initiatives such Gaia-X and Catena-X have been set up to help the various stakeholders communicate transparently. Meanwhile, in Japan Denso and NTT Data have been collaborating with the country’s Ministry of Economy, Trade and Industry to create an industry-wide data ecosystem for EV batteries that will interface with those in Europe and beyond. This is partly in response to proposed EU regulations that would see all EV batteries supplied with digital ‘passports’ containing a carbon footprint declaration.
A spokesperson for Denso told APTI, “The data initially required by the regulation is likely to include carbon footprint information covering the lifecycle of the battery, and information on due diligence covering environmental issues and human rights. However, at some point in the future we presume that a wider range of information will be applicable. This includes information on battery raw materials, recycled materials and remaining battery capacity.
“Such information is crucial because we assume that in the future, the distribution of data on the lifecycle assessment of automotive batteries could become mandatory. We believe that this will include highly confidential information, which will need to be managed accordingly.”
No plans have yet been announced to incorporate lifecycle assessments into vehicle emissions legislation, and there is active opposition to the concept. For example, last year the European Automobile Manufacturers’ Association (ACEA) released a paper outlining its position on LCAs. This document stressed that, in the association’s opinion, “LCA should remain a voluntary tool and cannot be used as a regulatory instrument … especially when taking into account the enormous complexity of vehicles and automotive supply chains.”
Many in the industry would agree with that at present. But things may be about to change. The European Commission recently announced plans for a common LCA methodology for cars and vans by 2025. The scheme would be voluntary for the foreseeable future, but shows that LCA is no longer a topic the industry can ignore.