Some 22 years after starting his career in Wolfsburg, Andreas Felske returned to the hub of Volkswagen R&D as head of transmission development in March 2020. It’s a role with a broad remit; meeting the technical needs of a brand sold on five continents and under countless regulatory regimes, during a particularly volatile period for the automotive industry.
“The biggest challenge at the moment is an increasing number of variants, due to different degrees of electrification and different legislations that have to be handled,” he says. “Of course, from the OEM’s point of view, a global harmonization of the homologation process and regulatory limits would help to reduce the technical variety.”
It’s a very different set of market demands from those he would have faced in 1998, but Felske has had a close involvement with the trends that have led to this point. Previous roles include engineering of automated manuals for cost-sensitive segments and the group’s ubiquitous DSG dual clutch transmissions. His return to Wolfsburg follows a hiatus in China – now a large, globally influential market in itself – most recently overseeing powertrain development for the FAW-Volkswagen Jetta sub-brand, which is aimed at first-time car buyers.
Buying habits have changed significantly in the meantime. Volkswagen introduced DSG with the Mk4 Golf R32 in 2003, aimed at overcoming traditional performance and efficiency compromises of automated transmissions. Within three years the group had sold half a million cars with the technology, and it doubled that volume 14 months later. Even in Europe, where three-pedal driving was the norm, it’s become a mainstream option for compact model lines – 40% of Golfs and 30% of Polos featured a DSG in 2018.
So developments are ongoing; the latest iteration of the modular transverse matrix (MQB) platform has enabled Volkswagen to adopt a shift-by-wire DSG system, controlled by a space-saving toggle switch. With no mechanical connection, the system can manage changes between forward and reverse gears with minimal shunt and reduced potential for damage to the powertrain. DSG is also the baseline technology for hybridization, enabling coasting functions for the eTSI mild-hybrid units in the Golf, and as P2 transmission for the Group’s expanding portfolio of plug-in hybrids.
This also diversifies the product offer: “In electrified powertrains the variety is much smaller than [we are familiar with] from conventional drivetrains. However, these new technologies come in addition to the current concepts, so we have an increased number of modules. Electric transmissions are also stressed in a totally different way; higher gear ratios and higher engine torques need to be combined with low noise requirements. This is a very challenging task for all transmission parts.”
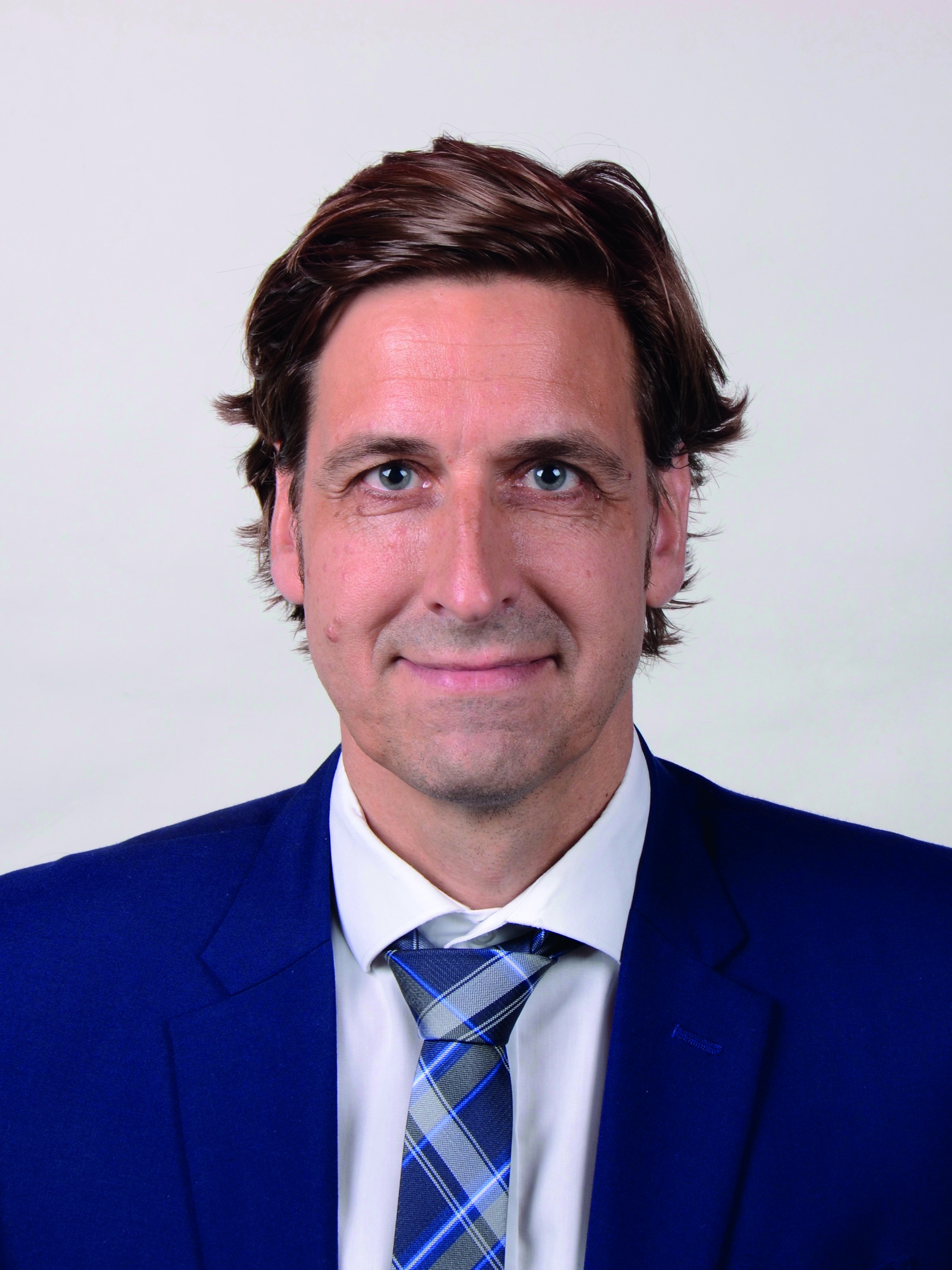
With a broad customer base, manual options aren’t being overlooked. The Passat debuted a new-generation, six-speed manual as part of an update last year, and the unit is earmarked for all except the heaviest-duty transverse car and van powertrains in the Group – applications previously covered by two transmissions, one of which was superseded completely. Its wider ratio spread contributes to a CO2 reduction of up to 5g/km at one end, and more responsiveness at the other. Production will take place in Barcelona, and in Argentina for the manual-weighted South American market.
Felske reveals more on the OEM’s product strategy: “Volkswagen Group has focused on modularity in the past and by this we try to cover the challenges [of differing electrification strategies and regulations]. All new transmission concepts should be designed to replace several old transmissions – that is our main goal for the upcoming years.”
These streamlining measures are aggressive. Last year Volkswagen targeted a 30% improvement in plant productivity by 2025, with plans to shed the least-popular 25% of powertrains in the meantime. Cost-effective solutions require shared components where possible, and Felske says advances in simulation tools are helping too.
“Simulation tools are evolving rapidly and almost every aspect of development is already covered. We see almost no broken parts on our test benches compared with earlier days because we have already established virtual test procedures over many years. The positive results let us believe in even more such effects in the future,” he says.
“While virtual development methods have a growing relevance, there will be a continued need for hardware prototypes and tests on rigs and roads. In some cases, like acoustics and haptics for example, with computing technology it is sometimes only possible to perform relative comparisons rather than absolute evaluations. Therefore we still have to carry out hardware tests
in vehicles.”
The Group also recognizes that solutions don’t mature effectively if development is siloed. Since 2015, it has sought closer partnerships with suppliers, sharing expertise from past projects and helping new technology come to market. The FAST (Future Automotive Supply Tracks) program offers access to senior decision makers and targets faster evaluation and commercialization. Felske sees this as a beneficial process for transmission development, too – a procedure that takes his already broad remit further still.
“In order to reduce the integration work of new transmissions in our cars, we try to integrate already developed components from our suppliers. Early prototypes and minimized development work help us comply with continuously decreasing development cycles. We are working very closely with our suppliers and we will intensify this work in the future as the suppliers take over more development responsibility,” he says.