Recent years have brought into harsh focus how fragile automotive supply chains can be. Spanning the globe, seemingly unrelated geopolitical events can have a huge impact on the availability of key components, placing the industry’s just-in-time production models in peril. Although semiconductors have recently taken the limelight, the reliance of most high-performance automotive traction motors on rare earth magnets has also come under scrutiny. Not only are the materials themselves subject to supply constraints but there is also an increasingly vocal conversation underway regarding their sustainability from both an environmental and a social responsibility angle.
The result is a growing requirement for power-dense motors that forgo such magnets. This is what was behind UK-based Ricardo’s development of the Alumotor concept, which not only does away with rare earths but also minimizes the use of copper. Ricardo’s project scope also includes industrial concepts for the motor and its integration into an EDU. APTI spoke to the company’s automotive and industrial technical authority head, Dr Jay Al-Tayie, and Simon Meredith, PEMD and transmission project engineer for performance products, to find out more about this novel motor architecture.
“The project started three years ago, when we were looking for a sustainable motor solution for the UK market,” says Al-Tayie. Permanent magnet motors are hard to beat from a performance and efficiency perspective “but they are expensive, not very sustainable and sensitive to supply chain issues,” he adds.
Making a rare-earth-free motor that comes close to the power density of PMSMs was going to be a tough undertaking, but Ricardo’s solution blends existing technology and novel engineering to achieve just that.
The Alumotor is a synchronous reluctance machine, a layout chosen for its potential for excellent torque output. “With switched reluctance machines, you obviously have to switch the phases, which is why they are noisy from both an audible and efficiency perspective,” explains Al-Tayie. “At low speed they are also quite hard to control and not very efficient. A synchronous reluctance machine is controlled very differently. You can run it very much like a normal permanent magnet machine, you don’t need rare earth elements or copper windings and, importantly, it is very robust. There is nothing really to degrade over time, unlike a PM machine where you may lose performance due to thermal and coercivity impacts.”
It is this robustness that means the Alumotor can be run at higher temperatures. With just steel and aluminum in the construction, there is nothing to be affected by heat (within reason). The only specific consideration is the insulation material coating the windings, but solutions are available. “As long as you select the right material, it is fine,” explains Al-Tayie. “Most motors do not go beyond 180°C and use class-H insulation, but you can go to class C, which is 220°C or higher. The advantage is you can run the machine hotter and increase power density without upping the size.” Furthermore, the Alumotor is designed to run at 800V, which means lower current and thus reduced losses. “Again, this lets you increase the power density,” he adds.
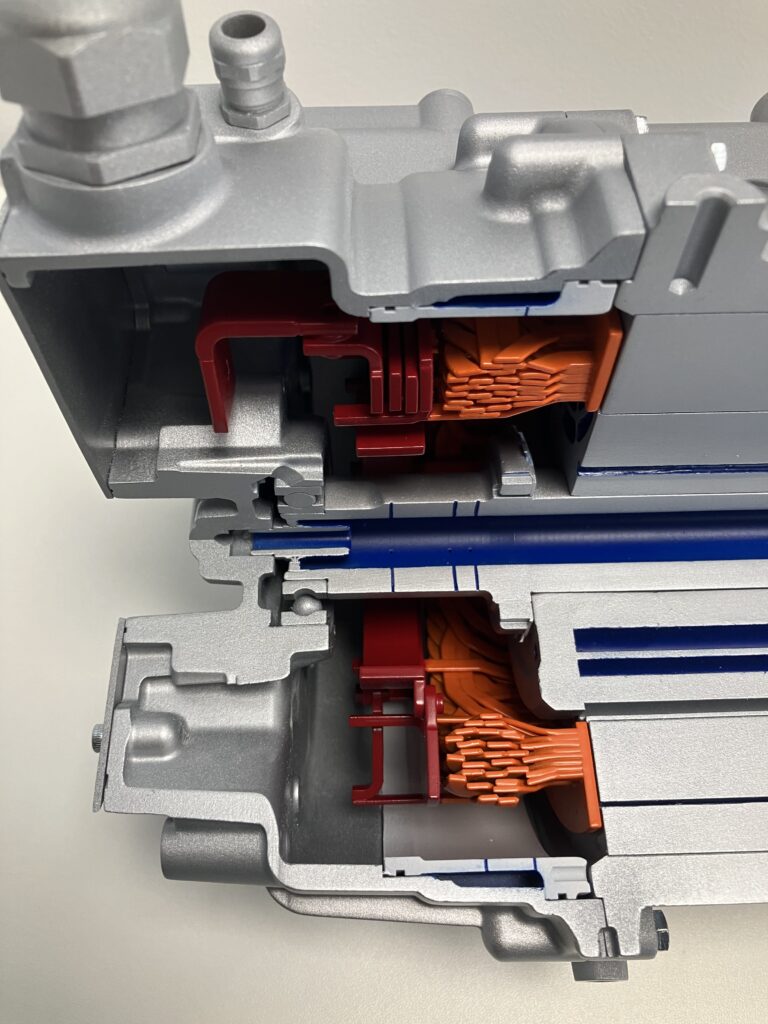
One of the standout features, and giving the motor its name, is the use of aluminum windings. “People ask, why aluminum? Because it’s more sustainable than copper, it’s cheaper and more readily available. With the technology we have developed we are able to use it without compromising power density, running at higher voltages and higher temperatures, for example,” says Al-Tayie.
Another novel feature of the design, beyond the use of aluminum, is the rotor topology and the form of the flux guides that direct the magnetic flux. “They are voids, just air,” says Al-Tayie. However, Ricardo also has a variant in development where these voids are filled with magnetic material. For machines that require lower power densities (but higher than the standard Alumotor), these could be ferrite magnets. Ricardo is working with partners on the development of materials with the same flux density as rare earth magnets but made from sustainable materials. This development would make the Alumotor design comparable to the best high-performance machines on the market.
The final piece in the Alumotor puzzle is the cooling system, which ensures that coolant can be placed directly where the greatest heat is generated. Both the rotor and the stator feature cooling channels, while spray jets also ensure the (dielectric) coolant can be directed onto the windings. “We are hitting it from every angle,” says Meredith. “We have conducted a lot of computational fluid dynamics and analysis work, which has given us a lot of cooling opportunities for the rotor and stator and means we can run them as hard as possible.”
Partner optimization
The Alumotor was developed as a joint effort by the UK-Alumotor consortium, led by Ricardo and involving partners Aspire Engineering, Brandauer, Warwick Manufacturing Group at the University of Warwick, Phoenix Scientific Industries and Global Technologies Racing (GTR). The breadth of expertise across the consortium has been a key enabler for the project. For example, Meredith highlights the work done in conjunction with Brandauer, which manufactures the steel laminations: “We’ve done a lot of technical work to make sure that the rotor is structurally sound and not going to break apart under its own stresses. These have been really delicately and intricately worked out and there has been a lot of collaboration with Brandauer on the stamping to make sure they can actually be manufactured. It’s been really good working with the consortium, to have those experts that you can lean on to understand what we can and can’t do and how feasible it is to manufacture things.”
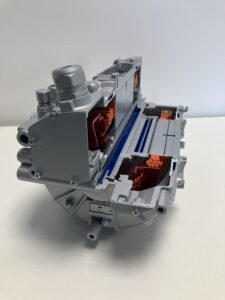
There are some manufacturing differences compared with a regular motor using copper windings. For example, the aluminum is softer and displays a greater level of spring-back when the hairpins are formed, but this can be accommodated within existing process technologies. “There has been a lot of careful experimentation to work out the parameters, such as making sure the bends are made in such a way as to not crack the enamel insulation,” notes Meredith. The welding of the windings also needs a different approach from copper, but again, there are established processes that can be adapted.
Full-circle approach
Early prototypes proved the concept and in 2022 Ricardo, in conjunction with its partners, commenced development of the current iteration of Alumotor, with support from Innovate UK’s Driving the Electric Revolution challenge fund, encompassing both the actual motor design and the supporting supply chain.
Ricardo is not immediately targeting the passenger car market with the Alumotor. Instead, it is looking to the LCV and off-highway markets, which would benefit most from its affordable and rugged characteristics. “While everyone is electrifying and everyone is going after copper and rare earth magnets, this is a great opportunity for an OEM customer to diversify and not get hit by the price rises that there are going to be,” concludes Meredith.
Further information about Ricardo’s electric vehicle solutions can be found here