Despite an ever-evolving game of supercar one upmanship, the car that has caused arguably the greatest stir in recent years isn’t the most powerful, or fastest, but it is certainly the most focused: Gordon Murray’s T.50.
His stated goal is a simple one: create the greatest driver’s car. Every element of the experience, from the steering feel to the gearshift, the weight of each control to the engine note, has been honed with this target in mind. In Murray’s words, “I have absolutely no interest in chasing records for top speed or acceleration. Our focus is instead on delivering the purest, most rewarding driving experience of any supercar ever built.”
But what engine for a car whose creator is looking to bookend the supercar era, the last truly analog driver’s car? As Murray put it to Automotive Powertrain Technology International, “I wanted a V12 from day one. For me, this is the most characterful and evocative engine layout and it fits our goal of producing the ultimate driver’s car.” Among the inspirations behind this call, he points out, “I am a great fan of the 1960s Ferrari 3-liter V.12 by Columbo,” which of course powered such legendary machines as the 250 and 365 GTB/4 Daytona.
However, the 3.9-liter, 65° V12 that will grace the rear of the T.50 is far removed from the V12s of old. Developed and manufactured by UK-based Cosworth Engineering and drawing heavily on the company’s motorsport heritage, it redlines at 12,000rpm and, with peak power of 663bhp, is a truly 21st-century engine.
Informal roots
According to Bruce Wood, MD of powertrain at Cosworth, there was no traditional tender process for the engine, more a series of informal conversations with Murray and his team, following which the project got underway in mid-2018. Murray admits that there were initially three companies considered, but “Cosworth was the obvious choice”. Not least because at the time of the meetings it was in the process of delivering the engine for the Aston Martin Valkyrie, a car with a different ethos but also requiring a very high-revving, naturally aspirated V12. It was of larger capacity (6.5 liters), with hybrid assistance, but its development made Cosworth unique as a manufacturer offering a roadgoing engine of this type.
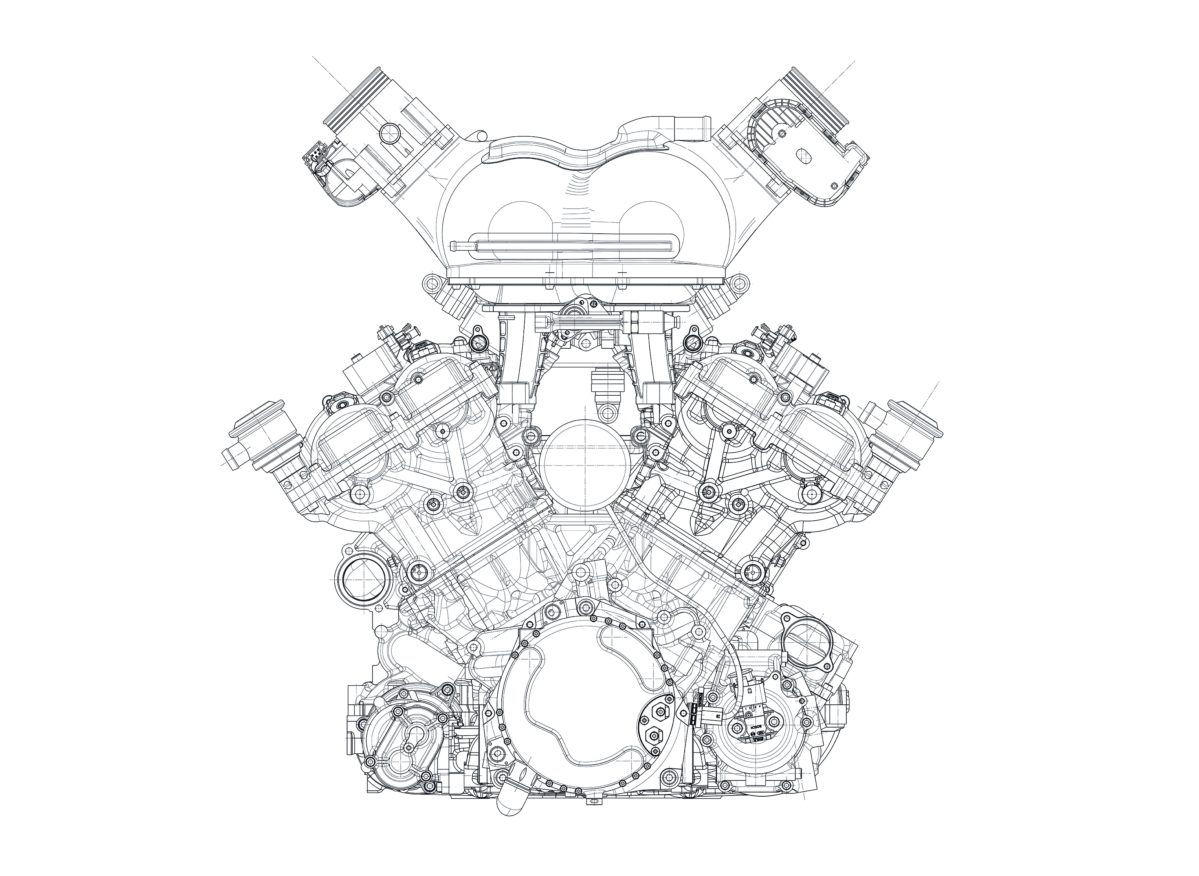
Neither was there a hard and fast engineering brief. Murray had settled on a capacity of around 3.9 liters, but, notes Wood, “Gordon has commented many times that it was not just about chasing numbers and that approach rather defines the car, or at least our role in it. It wasn’t a case of, here’s a table of numbers that everyone has to achieve, it was a more analog process than that, more emotion driven than just stark numbers.”
For example, he highlights, “We were clear we wanted to put a significant distance in terms of engine speed to anything else out there, which is where the 12,000rpm number came from. That meant power was never going to be a problem, because if you’ve got four liters running at 12,000rpm, you’re going to have enough power.” It should be noted that the power-to-weight target Murray initially set for the car was 600bhp/ton, which it comfortably exceeds.
Packaging and aesthetics
Factors such as the v-angle and crank height of the engine were driven by the packaging demands of the chassis. The placement of the exhaust, says Wood, consisting as it does of six individual primaries on either side, pushed the design toward the narrowest-possible bank angle, but, “there’s also an awful lot to fit in the center of the vee”. 65° was the ideal compromise while a crank center height of 85mm met the designer’s desires so far as CofG was concerned.
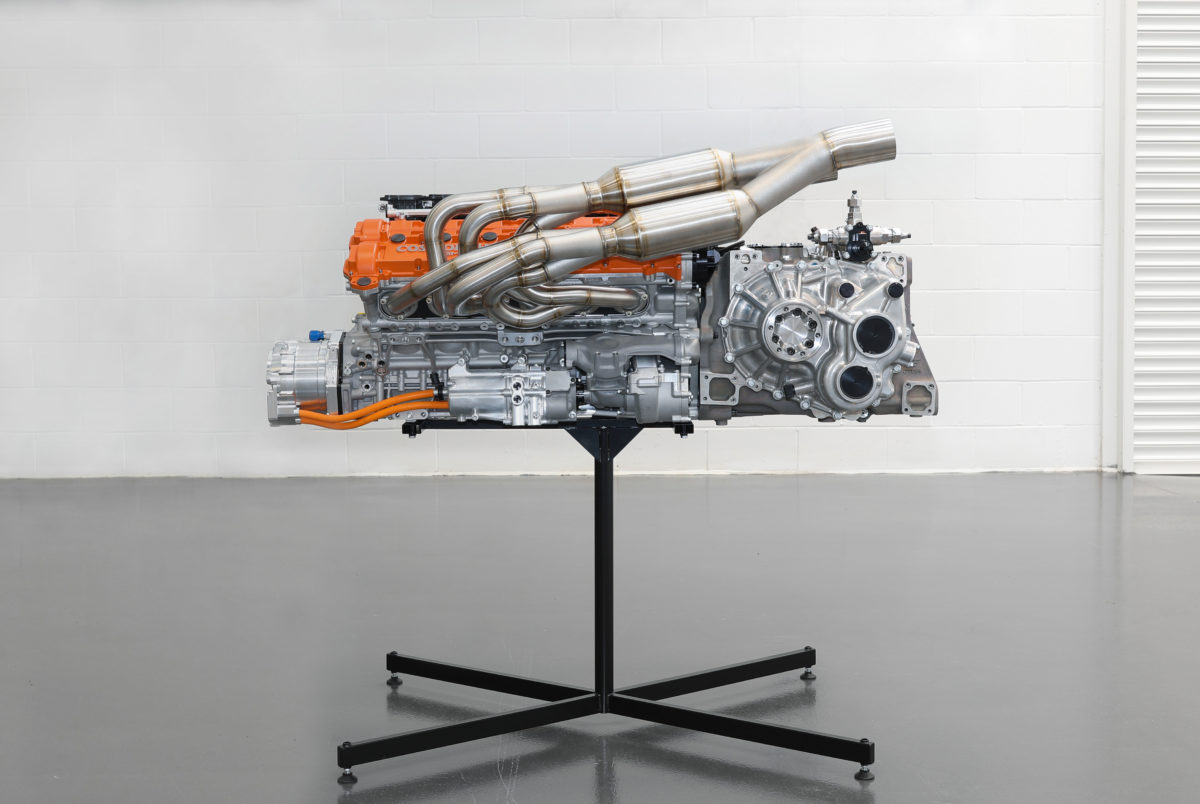
Murray wanted only the intake plenums and exhaust system to be visible from above when the two butterfly-hinged engine covers are open, highlighting attention to the aesthetic as well as engineering detail as a recurring theme running through his work. “Sometimes, it doesn’t seem to matter what an engine looks like,” muses Wood, who nearly pursued a career in industrial design. “For Cosworth that has always been very important; I’m a firm believer that good engineering also looks great. It was nice to have that opportunity where the appearance mattered as much to Gordon as it did to us.”
To achieve a clean look, there are no belt-driven ancillaries, with drive for the various pumps taken directly from the block. “It actually worked out quite nicely for us,” states Wood. “Sometimes, you end up with drives at both ends of the engine, the cam drive at the rear end to keep its noise away from the tub, and the auxiliaries at the front to accommodate underfloor tunnels. That’s very much the racecar style, but the T.50 doesn’t have tunnels, so we could put the pumps at the back of the engine as well and only use one drive.” Not only did this solution meet the aesthetic requirements, it also reduced the overall engine length and reduced weight. Murray confirms that all of the aesthetic targets were met: “I was after engineering art and Cosworth have delivered.”
High RPM reliability
To a company such as Cosworth, responsible for the first 20,000rpm Formula 1 engine, meeting the 12,000rpm target was within its comfort zone so far as the reciprocating components were concerned. Elements such as bearings are of course sized to meet the running life requirements (6,000km oil changes, and an 80,000km service life) while parts like the titanium connecting rods are straight out of the motorsport playbook.
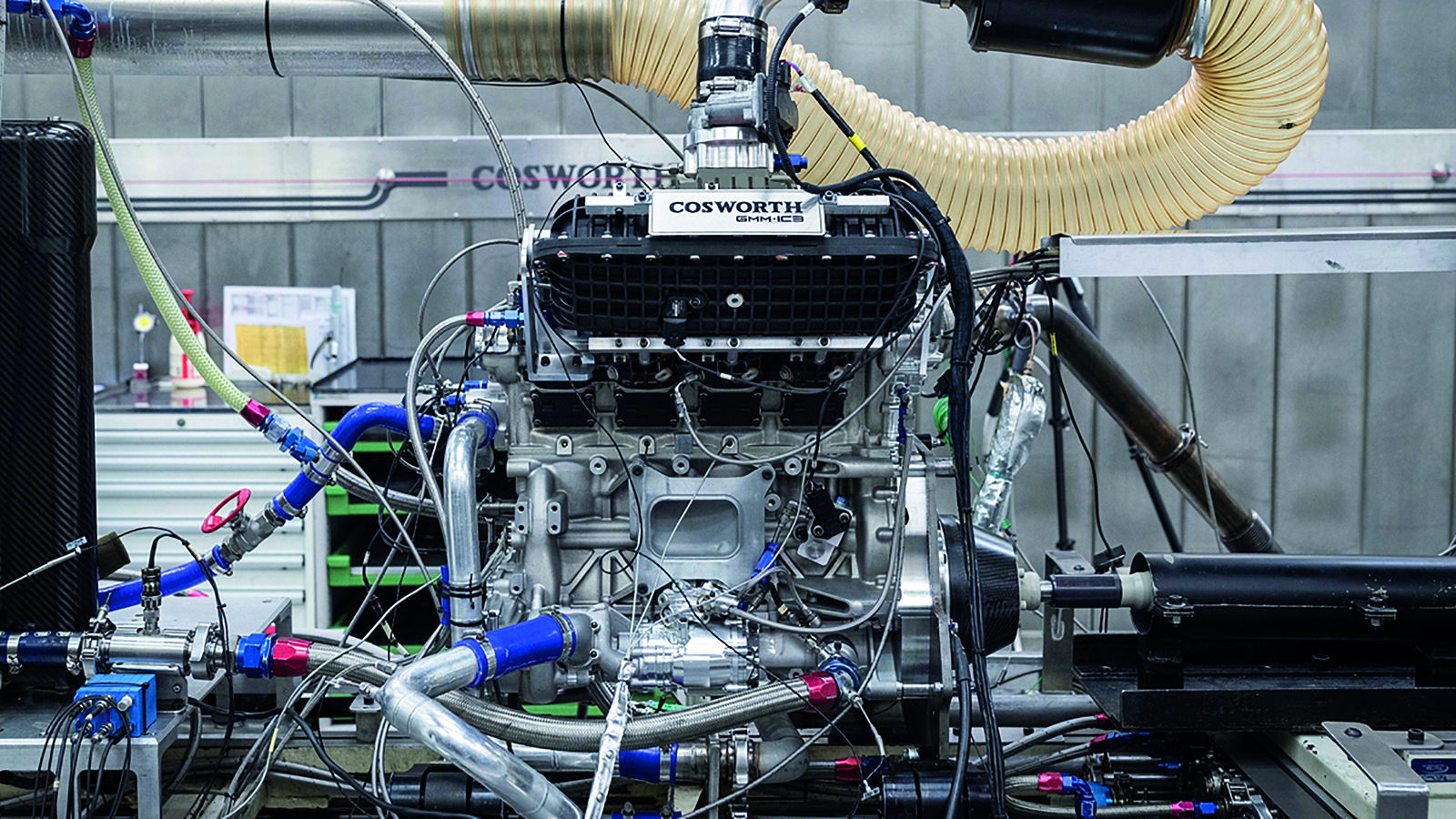
The addition of the Cosworth-developed 48V integrated starter/generator (IGS) had to be considered when it came to the crankshaft and block design, contributing as it does significant inertia at the nose of the crank. “That had to be factored in right from the start; the cranktrain dynamics were all modeled with that in place. The system uses a two-speed gearbox and there is a compliant element within that which is tuned to prevent the inertia doing anything nasty,” explains Wood.
The pistons are particularly noteworthy, being forged from a metal matrix composite rather than aluminum alloy. “Due to the engine speed and power density, and because it is a road engine, with quite a heavy ring pack, we felt we were right on the limit of what we could achieve with a monolithic material,” says Wood. Cosworth has been developing MMC pistons for several years, with materials partner Materion, and is comfortable with their use. Wood adds, “It certainly gives a nice bit of extra design freedom, though we make all of the pistons ourselves and boy do you get through cutting tools.”
The MMC pistons run in plasma-coated bores, a process that Cosworth completes in-house, having been using linerless blocks since its CA F1 engine of 2006. Wood states, “We’ve used it exclusively in race engines, and then more and more in road engine programs – particularly the higher-performance ones.”
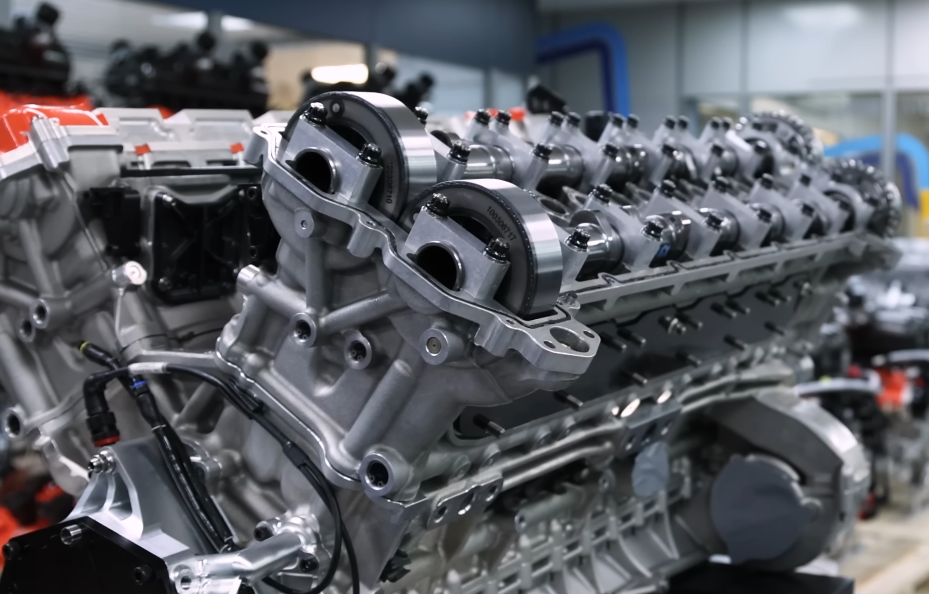
The engine runs conventional valve springs and, given its operating rpm, optimization of these and the rest of the valvetrain was vital to attaining reliability. “Clearly, the valvetrain is one of the bits where, if you’re going to have a failure, it is the most obvious place,” notes Wood.
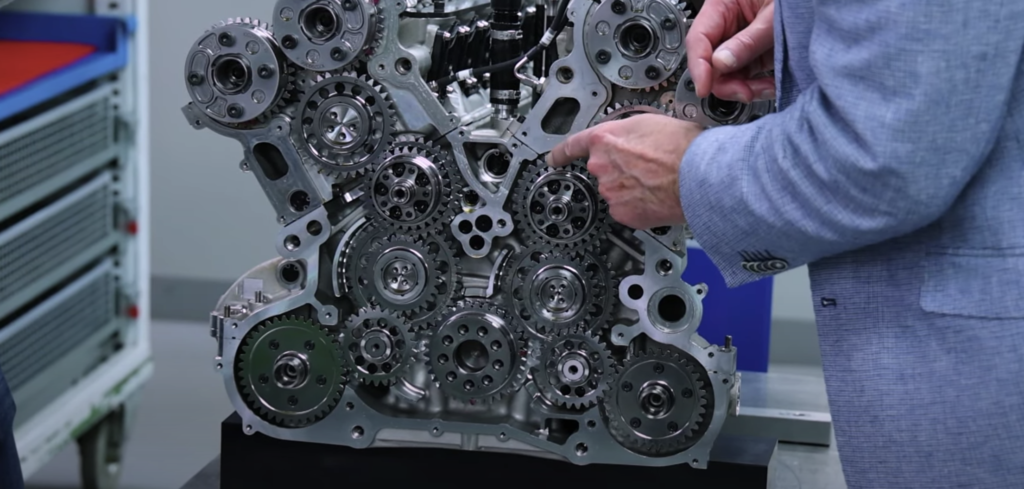
Of course, Cosworth has gone to great lengths to prevent this being an issue. Close attention has been paid to the cam profiles, particularly the transition between the ramps, while the valve springs – sourced from a long-time supplier in Japan – are made with triple vacuum remelted steel. Wood summarizes, “It’s all about getting the parts as light as humanly possible and then getting the springs right. They will always fail from an inclusion, they don’t just fail randomly, so you need that wire to be as clean as possible to prevent that. Then you spend a great deal of time finessing the cam profile. That was all a big, big piece of work to get right.”
The result of Cosworth’s efforts is truly impressive: a fully emissions-compliant, naturally aspirated engine that can rev to the stratosphere and packs just shy of 170bhp/l. The first GMA V12 engine fired up on the dyno in July this year and from now until customer car deliveries begin in 2022, Cosworth is focusing its attention on fine-tuning the calibration to ensure Murray’s demands for impeccable drivability are met. Wood concludes, “We’ve got a team of seven calibration engineers working on it and the first mule car [based on an Ultima chassis, as was the original McLaren F1 mule] is dedicated to calibration work. Even though we’ve ticked the box to say the combustion system can deliver on emissions, it’s still a two-year job to finesse everything to perfection.”
Injecting power
The GMA V12 employs port rather than direct injection and there are multiple reasons for this, says Wood. Most significantly, DI engines produce considerable volumes of particulates, with the filters required to remove these being large and heavy, something that wouldn’t fit with Murray’s gram-counting concept. Second, DI on a naturally aspirated engine is not great for power. Having a centrally mounted injector robs available valve area, and, as Wood points out, “port injection is lovely for power – you have fuel suspended in the air path for much longer than if you’re squirting it straight in the cylinder.”
With drivability a key consideration (71% of the engine’s maximum 467Nm of torque is available from 2,500rpm), not only was the calibration of the injection system and port design of great importance, but cam timing was also vital. Here, the deployment of a VVT system helped considerably, though Wood admits, “Getting VVT to work at 12,000rpm was the tricky bit.” One requirement to achieve this was a separate oil system for the VVT, which operates at a much higher pressure than the rest of the lubrication circuit.
Emissions
With the T.50 due to be sold across the globe, its engine has to be fully emissions compliant in the European and US markets. However, although this is a tall order, Wood says, “Our confidence going into this was hugely influenced by the Valkyrie, which has a much bigger bore. While that’s great for power, thanks to the piston speed and valve area, it is the enemy of emissions. The GMA has a smaller bore so we knew it would be easier, albeit we had to meet US federal emissions as well [which the Valkyrie didn’t].” On this last point, he notes that it is more the complexity of the OBD compliance element that is the challenge, rather than the actual bagged gas emissions.
Hitting the targets required a careful balancing act with the combustion chamber and port design, explains Wood. “The requirements for emissions are diametrically opposed to those you want for power. For the latter, you want laminar flow and controlled barrel turbulence in the combustion chamber. For emissions, you want mixed flow and as much turbulence as you can get in the chamber. So it is a conflict between the port shape you want for emissions and for power. Huge amounts of work went into that.”
Extensive development work was undertaken on a three-cylinder mule engine, representing a quarter of the V12, which, coupled with simulation, meant Wood and the team at Cosworth were comfortable they could hit the emissions targets. “We were running the mule six months before the V12, and that gave us early visibility that we could hit the emissions. That’s not to say it was easy, it certainly wasn’t.
Transmission
Coupled to the engine is an Xtrac-developed, 6-speed, H-pattern transmission. It is an entirely bespoke creation and as with every other part on the T.50, lightweighting is key. For example, in what may be a road car first, it utilizes a thin-wall cast-aluminum casing, and an expensive and complex manufacturing process favored in high-end racing transmissions.
In the context of a modern supercar, an H-pattern box may seem archaic, but again, Murray’s focus is on driver engagement rather than outright performance. “Maximizing the driver’s connection with the T.50 was central to our decision making. So, matching the V12 engine to an exquisite short-shifting manual gearbox was an easy decision to make. Xtrac has produced a very clever adjustable detent system to help develop the gear-change feel. We have built a gear-change development rig to enable workshop development of the gear-change feel. My target [for feel] is similar to the MK.1 Cortina GT feel and better than the McLaren F1.”