The size of the market for electric passenger vehicles has grown beyond the expectations of almost everyone. The car-buying public have been very accepting of the transition to electrified powertrains and have in general found them to exceed expectations. Many of those somehow disappointed with the EV experience state that charging is their primary problem, with sparse infrastructure, low speed of charging or a lack of energy carried on the vehicle (real or perceived). Those who do not travel very far and have the facility to charge at home are, by and large, very happy with their move away from the internal combustion engine.
Batteries continue to improve, in terms of reduced costs, increasing energy and/or power density, and the rate at which cells can reliably accept charge. At present the universal common factor in passenger car batteries is the use of some form of lithium chemistry. There is little doubt that there is steady improvement in lithium cell performance, but it is steady and incremental. Will there be an alternative that offers a major improvement in one or more important aspect of battery behavior, such as energy density, charging rate, durability or safety?
Compared with any kind of traditional battery chemistry, cells based on lithium are much better in terms of energy density, on both a volumetric and a gravimetric basis. The problem is that lithium is so attractive as an ingredient for commercial applications, where mass and volume are important, that it is almost impossible at present to conceive of a cell where lithium is not used. As the world slowly wakes up to the fact that the renewable energy revolution probably only works when we have large amounts of energy storage in our electricity distribution networks, the demand for lithium will increase.
The problem is that lithium is so attractive as an ingredient for commercial applications, where mass and volume are important, that it is almost impossible at present to conceive of a cell where lithium is not used.
It should come as no surprise that there is great interest in developing alternatives to lithium-based cell chemistries. This is not limited to academic institutions; some of the world’s biggest producers of electrified passenger vehicles are looking beyond lithium to a period in the future when lithium cells are not the only sensible choice.
Design choices
When engineers design or specify an energy storage system for an electric vehicle they do so based on several criteria and limitations. There is a target for the amount of energy to be stored on the car based on range requirement, a target for charge and discharge power, and targets for mass, volume, cost, durability and safety, among others. Balancing these against the available space and the distribution of that space on the car is part of the skill of making a successful EV.
There is, unsurprisingly, a lack of understanding of the limitations of battery design on the part of the general public, but many engineers unfamiliar with the behavior of batteries tend to think of the battery as simply an electrochemical analog of the fuel tank and expect it to behave as such.
Lithium is very reactive and relatively rare compared with other candidate metallic elements for cell manufacture. However, the combination of high electrode potential, with good energy and power density in both volumetric and gravimetric senses, has led to its universal adoption in automotive cells.
Before we embark on this brief discussion of some of the alternative technologies, we should understand that some types of cell, known as primary cells, are non-rechargeable and must be eventually discarded and, hopefully, recycled. Secondary cells are the category into which lead-acid and lithium-ion cells are grouped. They can be recharged electrically in a reversible process.
Lithium is very reactive and relatively rare compared with other candidate metallic elements for cell manufacture. However, the combination of high electrode potential, with good energy and power density in both volumetric and gravimetric senses, has led to its universal adoption in automotive cells.
Lithium-Sulfur and Lithium-Sulfur Dioxide
Well-known cell manufacturers such as Saft already produce lithium-sulfur cells on a commercial basis. Such cells offer rapid charging, greater energy density, lower risk of thermal runaway and reduced degradation of performance at extreme low temperatures.
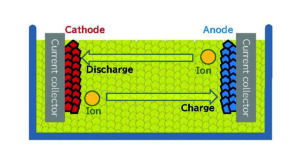
An additional advantage of this type of cell is the reduced reliance on cell materials that have a lot of ‘embedded carbon’ due to high energy use in manufacture, such as nickel and cobalt. The amount of carbon-dioxide generated in manufacture is much lower than for conventional lithium-ion cells, ensuring that the crossover mileage, where lifetime EV emissions become lower than those of an ICE-powered vehicle, is greatly reduced. Stellantis is known to be developing applications for lithium-sulfur batteries in conjunction with Lyten.
Commercially available cells have a gravimetric energy density of 400-500Wh/kg, which is in excess of lithium-ion cells used in leading passenger cars. Lithium-sulfur dioxide cells were previously considered to be primary batteries and non-rechargeable, but new work has revealed that they can be recharged, with Lim et al1 measuring incredible energy density that remained undiminished over 20+ cycles. It is still early days, but lithium-sulfur dioxide is showing promise as a secondary cell type.
Sodium Batteries
Sodium, like lithium, is a reactive metal, but it is very much more common. It is of course present as sodium chloride in seawater, and in Earth’s crust sodium is present at over 20,000ppm, compared with 20 for lithium. Sodium-ion is the cell technology closest to production that is not based on lithium. BYD, the world’s largest producer of passenger vehicles powered by electrified powertrains (by number, including battery EVs and ICE hybrids) is reportedly close to deploying sodium-ion batteries in production cars. Early development by CATL had, by 2021, produced cells with an energy density of 160Wh/kg, which is comparable to many production lithium-ion cells. Low-temperature performance is excellent, with 90% discharge rate retention at temperatures of -20°C.
Fast charging is, for various reasons, very attractive. It is a perceived advantage of IC engines that filling a fuel tank to capacity takes only a few minutes. Drivers don’t like the idea that they will have to break their journey for several hours, although that is often dependent on the charging equipment rather than the battery. However, CATL reckons that its sodium cells can be charged to 80% capacity in 15 minutes. Scaling this would give a 100% charge time of 18.75 minutes, giving a charging rate of 3.2C.
However, despite these advantages, CATL admits that the present level of energy density is not high enough and it plans to deploy batteries with a mixture of lithium-ion and sodium-ion modules. This is aimed at providing the best combination of charging rate, low temperature and energy storage within a given mass and volume limit. This mix-and-match approach to combining different electro-chemistries in a single vehicle battery pack is interesting because it offers the prospect of changing the proportion of lithium-ion and sodium-ion cells to suit different applications and requirements. Note that some of the companies developing solid-state cells are doing so based on sodium rather than lithium chemistries.
CATL reckons that its sodium cells can be charged to 80% capacity in 15 minutes. Scaling this would give a 100% charge time of 18.75 minutes, giving a charging rate of 3.2C.
Magnesium-Ion
Magnesium-ion cells are, on first inspection, quite unattractive compared with lithium-ion owing to poor gravimetric energy density. However, their volumetric energy density is high and research work on improvements in performance is already making inroads into the deficit against lithium-ion cells in terms of gravimetric efficiency.
Bae et al2 showed a measured gravimetric energy density of 412Wh/kg on research cells with an operating voltage of 2.8V, and Shah et al3 reported on the potential benefits and challenges in the adoption of this technology for automotive use.
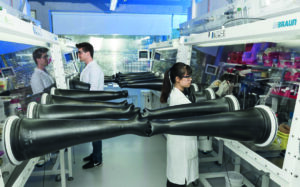
The fact that magnesium-ion batteries have a major theoretical advantage in terms of volumetric efficiency compared with lithium-ion bodes well. Small, light and inexpensive batteries will make packaging an easier exercise, offering greater freedom for vehicle designers and further lowering the financial barrier to EV adoption for end users.
Aluminum-Air
There has been some excitement about the prospects for aluminum-air batteries. Aluminum is abundant and there is already a mature existing supply chain that seems to be relatively free of controversy. The batteries offer low mass and great energy density, with 1,300Wh/kg being achieved as early as 2024.
However, they are primary cells and cannot be recharged, and therein lies their single biggest disadvantage: they must be replaced and the active material recycled when they have run out of energy. We not only require a stock of new batteries but we require them to be ubiquitously available if they are to be used for passenger transportation, in the same way that liquid fuels are presently. Just as there is an irreversible chemical reaction of fuels with the oxygen in air, the same is true for aluminum-air cells.
To compound this, vehicles would need to be designed for battery swapping rather than battery charging, and this represents a complete shift in vehicle design. While Nio is presently betting on battery swap technology (and has impressive automated battery swap stations), few other manufacturers appear to be following suit. When the battery is spent, the aluminum, now reacted to form aluminum hydroxide, must be processed back into aluminum. There is therefore an energy cost in recycling the spent cell material.
If you can reliably add 320 or 480km of range to your car in 5 or 10 unattended minutes, who will really want a much more expensive car with a 965km range? Range anxiety will melt away with the ubiquity of reliable fast charging.
However, one potential producer of this type of cell is confident that the running costs are comparable to other BEV energy storage when produced at scale. In terms of passenger transportation, the inability to recharge also means an inability to use regenerative braking, and this reduces the range per unit of energy for a given vehicle.
Metal-Oxygen
Metal-oxygen or metal-air cells (of which aluminum-air is one type) have generally been developed as, and considered to be, primary cells and suffer the same disadvantages as aluminum-air. However, in common with lithium-sulfur dioxide, some metal-oxygen cells have been reinvestigated in light of recent developments and discoveries and have been found to be rechargeable. Metal-oxygen types exhibiting rechargeability include lithium, sodium, potassium and magnesium. Kwak et al5 showed that lithium-air cells have achieved specific energies in the range of 500–1,000Wh/kg, with the closest other group being lithium-sulfur.
It may be a societal and grid-scale requirement for energy storage that leads to a commercialization of this type of cell after future work, but the results are already very impressive based on the work described by Kwak et al. The most promising technology involves an electrolyte composed of lithium salts dissolved in an organic solvent, although solid-state electrolytes are also being studied. The challenge for this type of cell is finding solvents that are suitable for the application, but the potential to store much more energy in a small volume and low mass provides the motivation for more research.
Solid-State
There is a degree of skepticism among a small, but significant, part of the car-buying public about the safety of BEVs, and much of this is due to the perceived safety problems of lithium-ion cells. Although rare, battery fires garner negative publicity and nothing travels as far or as fast as bad news.
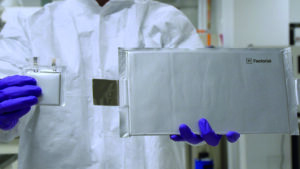
Solid-state materials promise considerably safer cells, and are much less prone to thermal runaway in the event of vehicle damage or overcharging. Lithium-ion cells with solid (rather than liquid) electrolytes are attracting a lot of R&D expenditure and interest. Toyota, the most visible of the long-established OEMs developing solid-state cells, is spending a lot on development and has recently entered into a partnership with Idemitsu to develop mass-produced solid electrolytes, aiming for commercialization in the next four to five years. However, BMW, Nissan-Renault, Volkswagen, Ford, Daimler, Stellantis and others are also known to be committed to the technology, often through major investment in existing companies whose business is the development of these products.
In terms of the booming Chinese EV sector, major players such as Dongfeng and Nio both seem committed to introducing models fitted with solid-state cells. BYD, whose sales volumes of electrified powertrains (EV and hybrid) outstrip all others, has a substantial number of patents concerned with solid-state batteries and seems likely to introduce them in the future.
Summary
There are several factors prompting the development of different cells. Worries over lack of access to lithium are important, but there are also other drivers. One of the factors common to many of the alternative cell technologies is increased energy density and the capability to charge at high rates. When adding energy to a battery, the limiting rate is dictated by cell technology and the energy capacity of the cell. Thinking about a battery simply as an electrochemical analog of a fuel tank is too simple. The size of a battery has a direct effect on the rate at which it can be charged, and many engineers don’t yet understand that. Cells that can be charged at a faster rate can produce a relatively small, light battery that will potentially remove the range anxiety that puts people off buying electric vehicles.
Higher energy density and increased charging rates will mean that range anxiety will become less of a concern. If you can reliably add 320 or 480km of range to your car in 5 or 10 unattended minutes, who will really want a much more expensive car with a 965km range? Range anxiety will melt away with the ubiquity of reliable fast charging. However, the ability to charge quickly requires the charging infrastructure to keep pace with battery technology. It will be fascinating to see the progress in battery technology in the coming years.
References
1) Lim H-D, Park H, Kim H, Kim J, Lee B, Bae Y, Gwon H & Kang K, A New Perspective on Li-SO2 Batteries for Rechargeable Systems. Angewandte Chemie International Edition, 54(33) (2015)
2) Bae J, Park H, Guo X, Zhang X, Warner J H, & Yu G, High-performance magnesium metal batteries via switching the passivation film into a solid electrolyte interphase. Energy & Environmental Science, Volume 14 (2021)
3) Shah R, Mittal V, Matsil E & Rosenkranz A, Magnesium-ion batteries for electric vehicles: Current trends and future perspectives, Advances in Mechanical Engineering, Volume 13, Issue 3 (2021)
4) Yang S & Knickle H, Design and analysis of aluminum/air battery system for electric vehicles, Journal of Power Sources 112 (2002) 162-173
5) Kwak W-J, Rosy D S, Xia C, Kim H, Johnson L R, Bruce P, Nazar L, Sun Y-K, Frimer A, Noked M, Freunberger S & Aurbach D, Lithium-Oxygen Batteries and Related Systems: Potential, Status, and Future, Chemical Reviews (2020), vol 120