Toyota has further refined its liquid hydrogen-fueled Corolla race car, which competed in the Autopolis round of the Super Taikyu series on July 29 and 30. Following a fire during testing earlier in the year, the team modified the layout of the fuel system prior to the Fuji 24 Hours Race at the end of May. Toyota began testing a liquid H2 version of the car in 2022, following the successful running of gaseous variant over the preceding two years.
Reliability concerns with the liquid H2 pump (required to operate at -253°C), meant the team had to plan in two pump changes over the 24-hour Fuji race, a process which required draining the system of H2, filling with nitrogen, replacing the pump, then refilling with H2. The first pump change took four hours!
Following a pep talk from Akio Toyoda, the second change was cut to three hours. Clearly, having to change pumps twice during a 24-hour race was less than ideal and Toyota has spent the past two months trying to improve this.
The result is a pump system which can run for 30% longer under similar conditions. One of the main challenges is that lubricating oil cannot be used to reduce friction in the pump, as it contaminates the hydrogen. Toyota’s solution was to introduce a buffer system, to reduce demand on the pump gear drive unit and hopefully allow it to complete a five-hour race without the need for a change.
Weight savings have also been made, with Toyota trimming 40kg out of the car through the optimization of various elements of the H2 system and, significantly, a reduction in fuel pressure enabling a smaller pump drive battery to be used. As a result, the vehicle now weighs 1,910kg compared to the 1,950 kg it weighed during the Fuji 24 Hours Race in May.
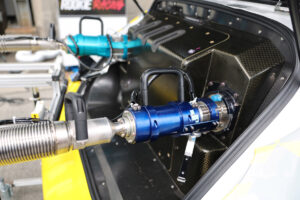
Refueling revisions
Toyota also turned its attention to refining the refueling rig used at the race. It succeeded in reducing the weight of joints and flexible hoses for the mobile liquid hydrogen station that was developed jointly by Iwatani Corporation and Toyota. Since the joint and flexible hose weight puts a burden on the crew that fills the vehicle with hydrogen, reducing their size and weight is an important consideration for future commercial applications. The weight of the filling joint was cut from 8.4kg to 6.0kg and the return joint from 16.0kg to 12.5kg; this was achieved by eliminating the connection cover and changing the components that do not come into contact with hydrogen from iron to aluminum. The flexible hose on the return joint side was also changed to a thinner hose, reducing the weight from approximately 4kg to 1kg.
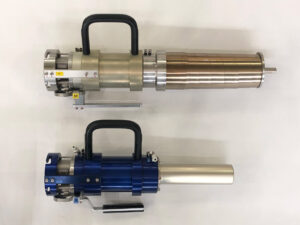
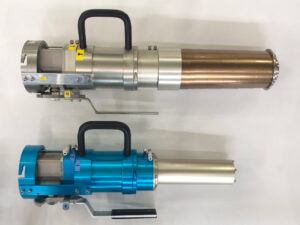
Both pictures show the joint used during the Fuji 24 Hours Race (top) and the improved joint (bottom).
Until now, all hydrogen filling operations for the hydrogen-powered Corolla, such as opening and closing the filling valve and stopping filling when the hydrogen reaches full capacity, were performed manually. For the Autopolis race these operations were automated via an electronic control system.
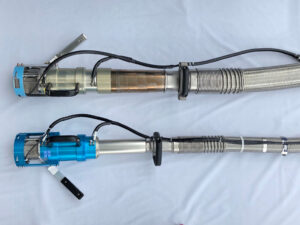
A high-flow-rate filling-side stop valve developed by Fujikin Incorporated was also installed onto the filling port of the liquid hydrogen tank. Larger valves are harder to seal, however Fujikin was able to create a reliable system with hydrogen filling time reduced to approximately one minute, down from 1 minute 40 seconds at the Fuji 24 Hours Race.
Unfortunately, as yet undisclosed reliability issues with the car meant it retired after 91 laps of the five-hour event.
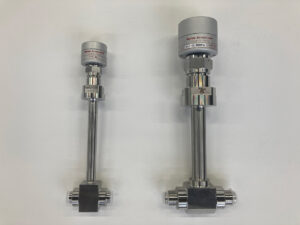
Pre-improvement (left) and post-improvement (right)