This approach, known as the dual hardware-in-the-loop (dual HIL) platform, enables simultaneous testing of different WEC components to provide an understanding of how these parts interact.
Despite significant advancements in WEC technology, challenges remain, particularly in ensuring device reliability and the performance of the power take-off systems. Rig testing is important in addressing these issues before WECs undergo operational tests at sea, thereby improving their chances of success, the project states.
The dual HIL platform consists of two independent rigs that operate simultaneously to test two WEC subsystems. These include a drivetrain test rig and a structural components test rig.
Initially constructed as part of EU IMAGINE project, the drivetrain test rig has been upgraded through Impact. It tests linear and rotary power take-offs (PTOs) for various WEC types and emulates different grid conditions and points of common coupling. The new capabilities of this rig were demonstrated by characterizing the performance of an off-the-shelf drivetrain, including a rotary geared generator and grid-side converter.
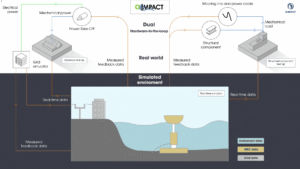
Designed and constructed under the Impact project, the structural components test rig evaluates the integrity of mechanically stressed components such as mooring systems, dynamic power cables, joints and seals. This rig has already been employed to test the belt of Carnegie Clean Energy’s CETO 6 WEC.
The dual HIL platform’s two rigs run concurrently, targeting different WEC parts. Feedback data from these tests is fed into a real-time simulator and used collectively with environmental data to inform subsequent tests.
“The Impact project resulted in a new testing infrastructure and applicable methodologies that can be used by WEC developers to accelerate their technology development pathways and find out eventual criticalities associated with a subsystem or even at WEC level,” said Giacomo Alessandri from VGA, the project’s coordinating partner.
“The rigs have been designed and proven to be as flexible as possible, to address tests of different WEC and subsystem types, therefore adding a missing brick at the EU level. These capabilities will play a fundamental role in the near future, especially for developers requiring de-risking activities prior to the deployment of sea-going prototypes.”
The Impact platform will continue its development as part of the Structural Wave Energy Equipment Test (SWEET) Lab at VGA’s facilities in Deruta, Italy.