The sophisticated 738m2, two-story facility is equipped with cutting-edge testing technology such as advanced simulation capabilities for road grades, load and wheel slip and robotic driving systems capable of handling both manual and automatic transmissions.
Jonathon White, VP of engine business engineering, emphasized the significance of the new facility: “This center enables us to develop and test a broader range of vehicles and machinery powered by hydrogen, renewable natural gas, advanced diesel or battery-electric. It is a key element of our destination zero strategy, aimed at reducing greenhouse gas emissions and improving air quality while aiding our customers in their transition to cleaner energy solutions.”
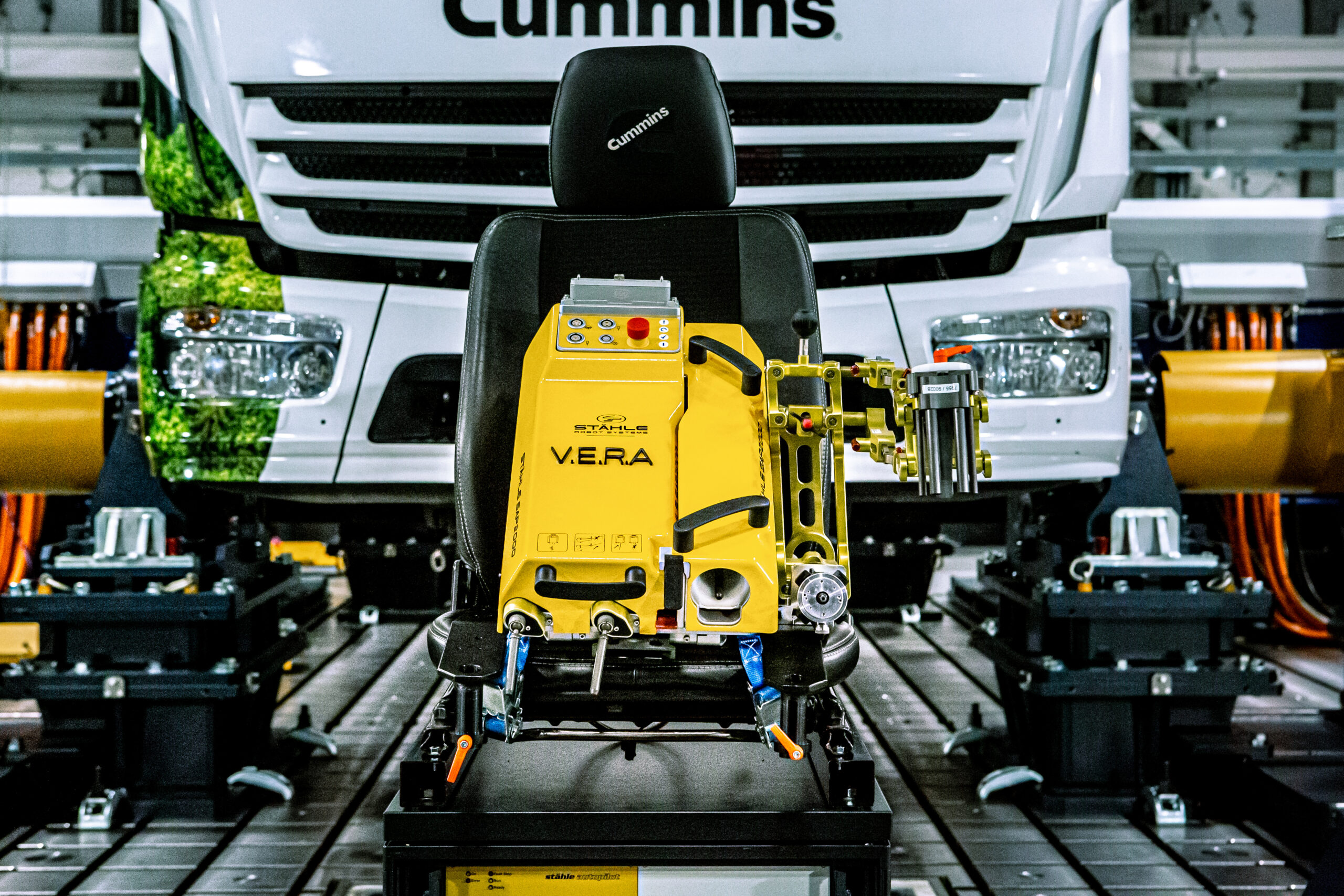
The facility represents a major upgrade for Cummins’ engineers, who are now learning how to harness the advanced dynamometers to analyze chassis-installed powertrains. This advance enables the development of full drivelines for a variety of applications, from compact SUVs and 44-ton trucks to double-decker buses and off-road machinery for construction and agriculture, with both two-wheel and four-wheel drive options.
White further noted, “Our extensive powertrain engineering expertise is driving the adoption of cleaner technologies, enhancing driveability, performance, efficiency and sustainability while keeping operational costs manageable. Additionally, the facility is designed to meet forthcoming regulatory standards, such as Euro 7 and CO2 heavy-duty vehicle regulations.”
Each of the dynamometers features energy recovery systems that generate electricity for use across the Cummins site, reducing the strain on the local grid. The facility also utilizes rainwater harvesting to minimize water consumption, reflecting a system already implemented at the company’s engine plant.
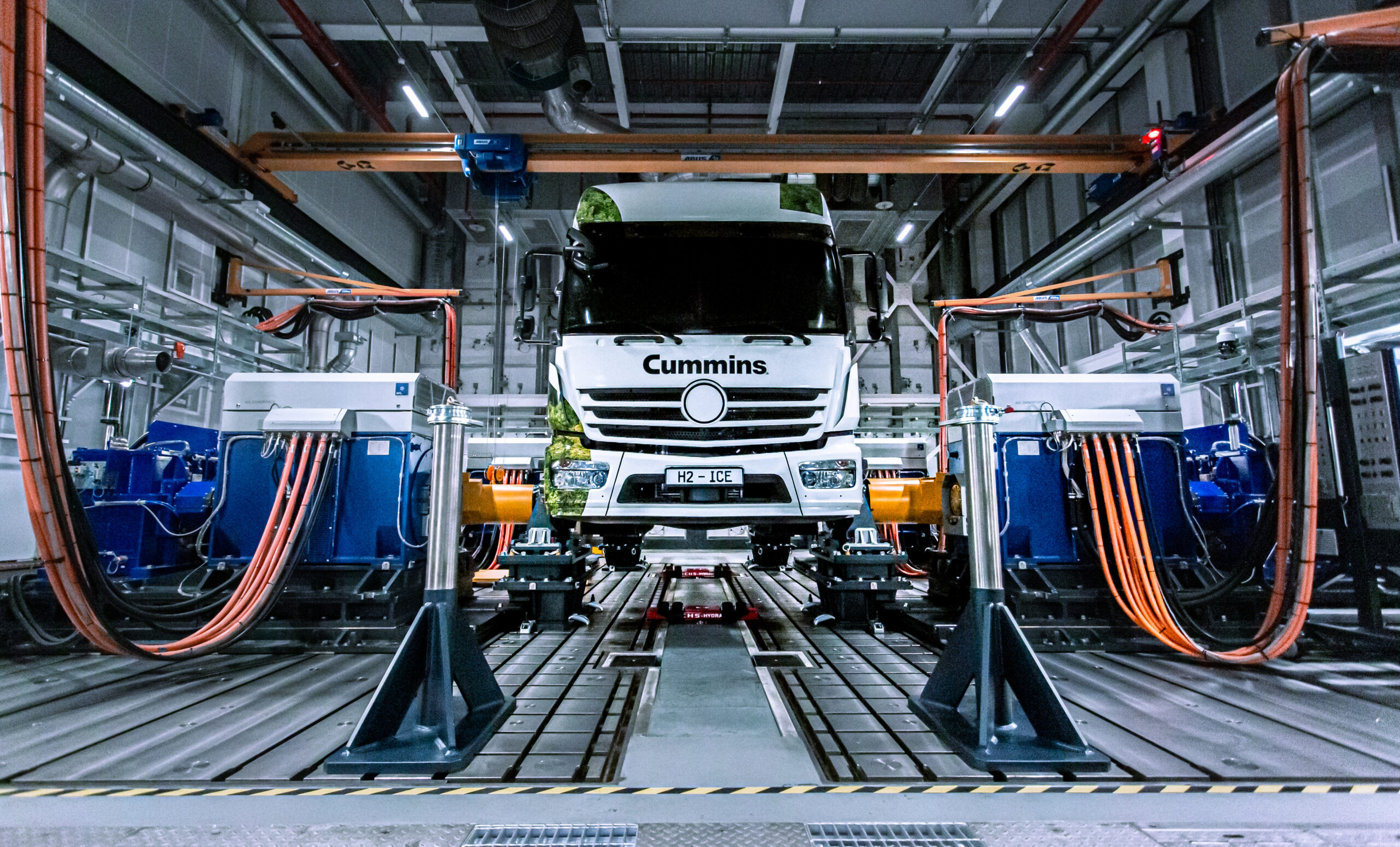